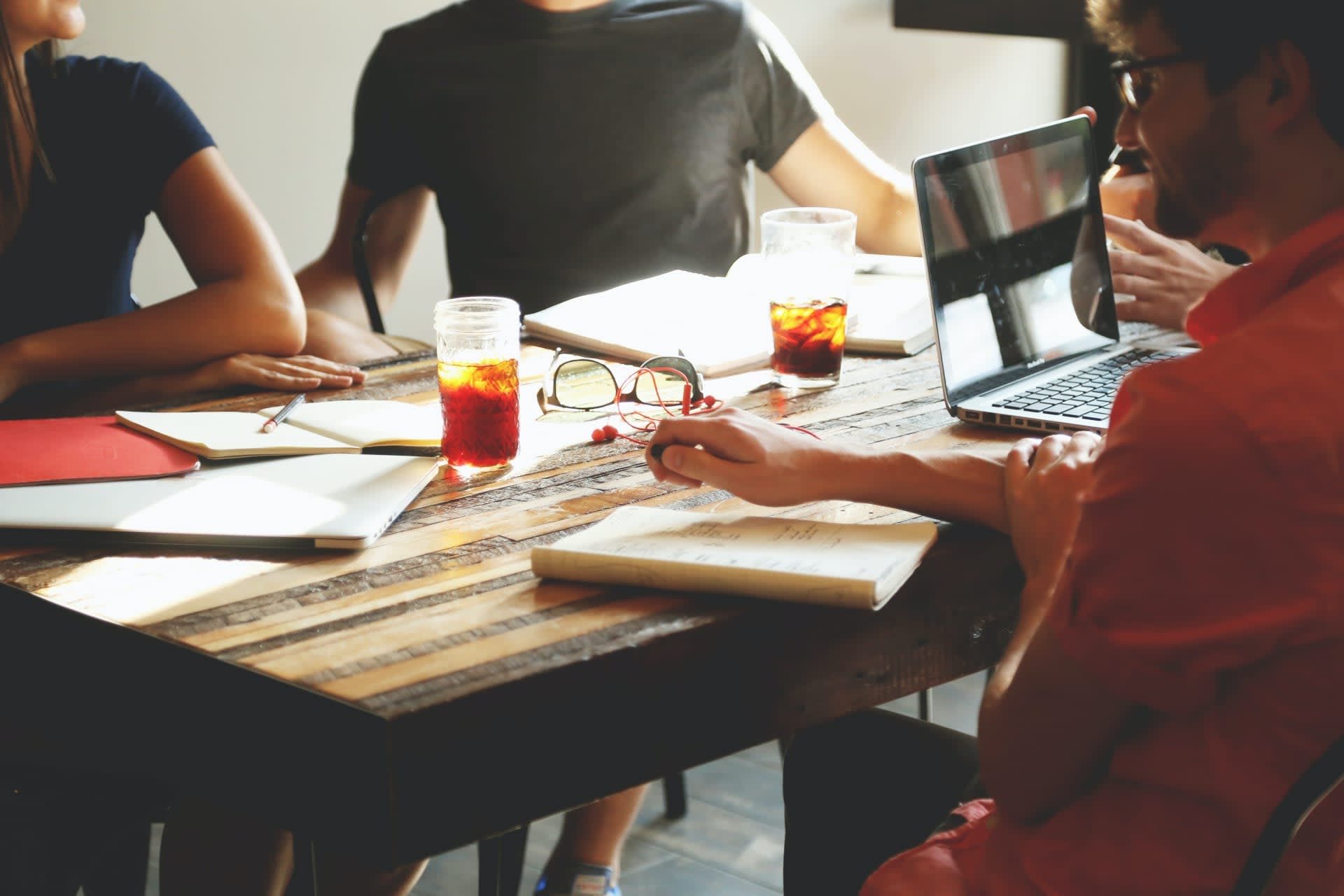
Operations Manager
On-site- Xanthi, Anatolikí Makedonía kai Thráki, Greece
Lithos Cell Engineering
Job description
Sunlight Group Energy Storage Systems is a world-leading technology company and provider of innovative industrial and off-road energy storage solutions, with 30+ years of experience. We specialize in the development and production of lead-acid and lithium-ion batteries for industrial mobility, leisure mobility, and ESS applications. These products are manufactured and assembled in Sunlight’s state-of-the-art facilities in Greece, Italy, Germany, Israel, and USA, and distributed to more than 115 countries.
Driven by our commitment to inspire our people and unlock their potential, and steadfast in our commitment to Diversity, Equality & Inclusion, we have created an agile and innovative environment that promotes open communication and collaboration, while offering continuous learning and development opportunities to the 3,100+ people we employ across the organization.
Keen to further empower our team by onboarding more talent, we are currently looking for a passionate Operations Manager to join our IPCEI team and lead the manufacturing team of our Lithium Cell Megafactory in Xanthi. This is a key role for our operations, tightly linked to the strategic pillars of Sunlight. The manufacturing team led by the Operations Manager, is expected to have exponential growth, both on skills and in size. Battery cell manufacturing is a highly complex operation in regard to process & equipment and we need a talented operations manager to be the enabler of the R&D campaigns by coordinating all the production aspects of these campaigns, including but not limited to organization structure, production schedule, materials and Opex. This is a global role in a very demanding manufacturing environment which will open numerous career opportunities to advance further in the battery manufacturing industry, the fastest growing industry in Europe and globally, currently & for the years to come.
Key activities and responsibilities of this role includes:
- Decides on the required resources and create organizational structure for the Megafactory manufacturing team
- Sets goals & priorities for the Megafactory manufacturing team
- Develops and manage the Megafactory budget, monitor expenses, and implement cost-saving initiatives without compromising quality or safety
- Develops and implement strategies to maximize operational efficiency, minimize downtime, and optimize production processes
- Plans and organizes the production schedule to enable R&D campaigns
- Ensures compliance with environmental, health, and safety regulations to maintain a safe working environment for all employees
- Selects equipment and ensure its timely and proper maintenance
- Drives the implementation of lean manufacturing principles and best practices to streamline operations and reduce waste.
- Establishes Technology Transfer & Training package across production
- Implements 5s methodology across production
- Monitors the production processes and adjust schedules as needed
- Monitors productivity rates and product standards and implement quality control programs
- Ensures damaged equipment gets repaired on time
- Liaises with different departments, teams and companies, e.g. suppliers, managers, clients
- Works with managers to implement the company's policies and goals
- Supervises and motivate the entire Megafactory production team
- Reviews performance of supervisors and identify training needs
Job requirements
- Bachelor's degree in Engineering, Manufacturing, Operations Management, or a related field. Advanced degree preferred.
- Proven experience in a leadership role within a manufacturing environment, preferably in the battery industry.
- Demonstrated expertise in operational management, including production planning, process optimization, and lean manufacturing principles.
- Exceptional communication and interpersonal skills, with the ability to collaborate effectively with cross-functional teams.
- Understanding of quality standards and health & safety regulations
- Knowledge of performance evaluation and budgeting concepts
- Excellent leadership and team management skills, with the ability to inspire and motivate a diverse workforce.
- Strong decision-making skills and a results-driven approach
- Fluency in English (verbal & written) is a must
- EU permit and fulfilled military obligations – where applicable
or
All done!
Your application has been successfully submitted!